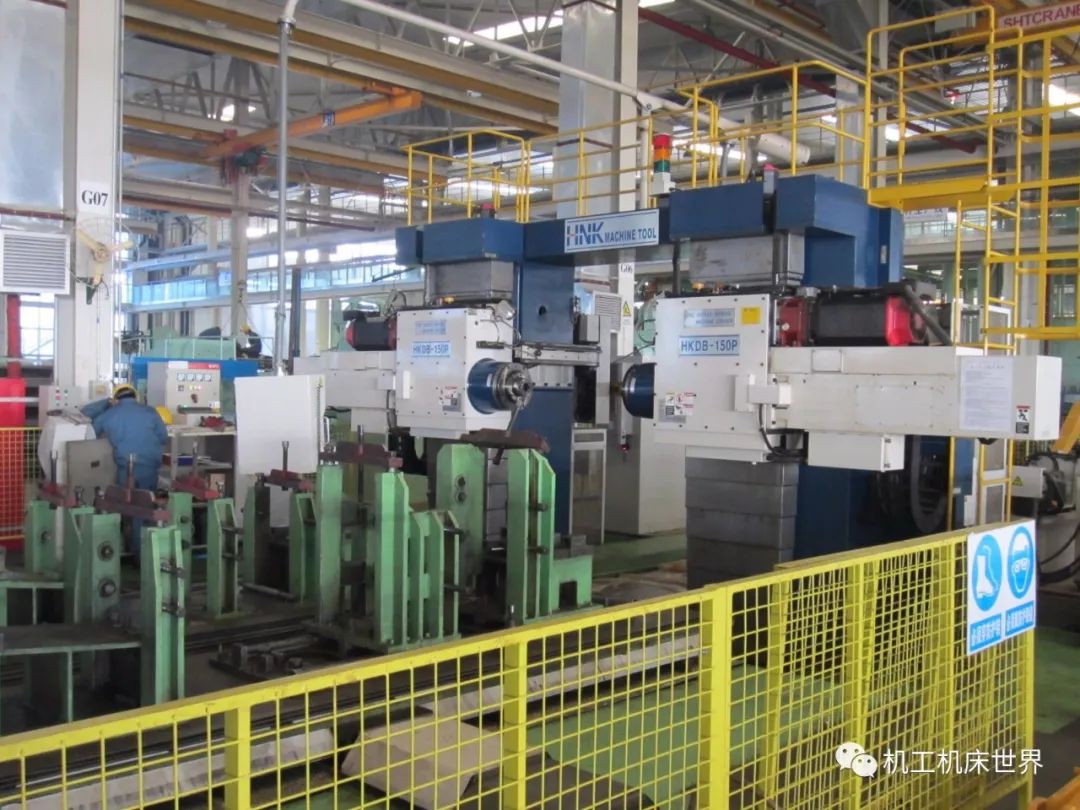
动臂、斗杆都为箱体类结构,以21T动臂为例,动臂长度为6m,宽度只有0.5m,在焊接过程中因组对间隙、焊接顺序及约束不充分等因素造成动臂的收缩和弯曲变形。后工序加工一般的工艺路线是:焊接后使用划线机划线,在加工中心上频繁试刀后进行加工,出现工序增加和瓶颈工序问题。公司引进雷尼绍测量技术,通过在线测量并打印后,手动调整修正值进行加工的先进方法,解决了加工中心的瓶颈工序问题。
RMP60测头系统是雷尼绍公司推出的性价比比较高的测头,它与数控机床连接应用,可以实现工件测量、刀具测量的功能,可以缩短90%的机械加工辅助时间,并消除由于设定误差造成的产品报废,是智能制造的“眼睛”。测量原理如图1所示。

如图2所示,在线测量设备由配备测量系统接口的数控加工中心5、需要加工的工件挖掘机动臂7和斗杆6、雷尼绍RMP60测头4、带有加工中心测量宏程序的数控面板3、雷尼绍RMP60接收器2、打印机1组成。
首先把雷尼绍RMP60接收器与加工中心数据线连接,保证数据的传输;其次把雷尼绍RMP60测头放入加工中心刀库后,与雷尼绍RMP60接收器进行配对。最后把打印机与加工中心相连,保证数据的打印。
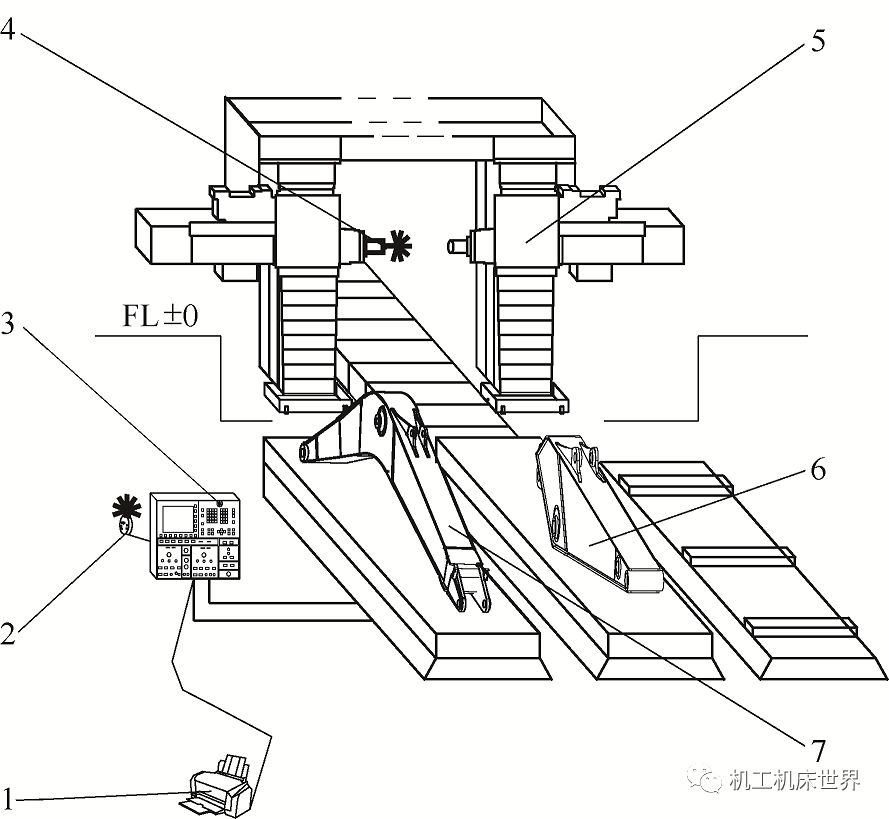
1.打印机 2. 雷尼绍RMP60接收器 3.数控面板 4.雷尼绍RMP60测头 5.数控加工中心 6.斗杆 7.动臂
在加工中心数控面板编制雷尼绍基本功能宏程序,主要内容为测头的标定、内孔测量、开启与关闭等基本功能的实现。然后在加工中心数控面板编制加工中心测量宏程序,主要内容是先定义各支座孔中心距坐标进行变量赋值,测头测量后的值赋给机床变量,赋值后的机床变量与标准值和偏差值进行计算,计算后打印测量日期、测量目标、测量方向、测量值、超差值及偏差值。然后再根据打印数据和加工余量手动调整各支座孔中心距坐标数值。
挖掘机动臂、斗杆焊接后,需要对各支座孔进行镗孔,来保证各支座孔的中心距坐标在公差范围内,焊接后放置在配备测量系统接口的数控加工中心上,定位装夹后支座孔中心距坐标数值需要收集。动臂、斗杆在加工中心装夹后,从数控面板调出测量宏程序和测头对动臂、斗杆各位支座中心距坐标进行测量。
测量宏程序主要内容:先使用加工中心定义每个支座中心距在XY方向的系统变量,测量宏程序中引用每个支座中心距在XY方向的系统变量来编制每个支座中心距的测量程序,然后加工中心使用测头对每个支座中心距在XY方向坐标值进行测量,完成后再赋值与预先定义的系统变量里,完成使用测头对支座进行测量的动作。
测量程序如下:
%O1301(J213-62A-100000)(TAN TOU)
( WORK HOLE POS. CHECK RENISHAW)
(PALLET NO.01)
M06T40
M0
G90G56
G100
#550=113.0(ZP1)
#552=111.25(ZP2)
#554=70.5(ZP3)
#556=113.0(ZP4)
#558=85(ZP5)
#560=0(XP01)
#561=0(YP01)
#562=290.0(XP02)
#563=0.0(YP02)
#564=2100.0(XP03)
#565=275.7(YP03)
#566=2493.01(XP04)
#567=-199.7(YP04)
#568=3127.01(XP05)
#569=0.0(YP05)
G91G28Z0
N0(G56 WORK OFFSET)
(P01)G0G90G56X#560
Y#561
M61
G04X1
G43H40Z[#550+50.]
G65P9810Z[#550-8]F2000
G65P9814D75.Q10.S3(S3=G56)
G65P9810Z[#550+20.]
N1(P01)G0G90G56X#560
Y#561
G43H40Z[#550+50.]
G65P9810Z[#550-8]F2000
G65P9814D75.Q10.
G65P9810Z[#550+50.]
G53
#560=#135(XP1)
G53
#561=#136(YP1)
G53
N2(P02)G90G0X#562
Y#563
G43H40Z[#552+50.]
M61
G04X1
G65P9810Z[#552-8]F2000
G65P9814D75.Q10.
G65P9810Z[#552+50.]
M62
G100
G49
#562=#135
#563=#136
G04X1
N3(P03)G90G0X#564
Y#565
G43H40Z[#554+50.]
M61
G04X1
G65P9810Z[#554-10]F2000
G65P9814D70.Q10.
G65P9810Z[#554+50.]
M62
G100
G49
#564=#135
#565=#136
G04X1
N4(P04)G90G0X#566
Y#567
G43H40Z[#556+50.]
M61
G04X1
G65P9810Z[#556-5]F2000
G65P9814D85.Q10.
G65P9810Z[#556+50.]
M62
G100
G49
#566=#135
#567=#136
G04X1
N5(P05)G90G0X#568
Y#569
M61
G04X1
G43H40Z[#558+50.]
G65P9810Z[#558-10]F2000
G65P9814D80.Q10.
G65P9810Z[#558+50.]
M62
G100
G49
#568=#135
#569=#136
#544=#5262
G04X1
M00
M98P1304
M00
G56G90G0X3500
M06T02
G100
G56G90G0X0.
M98P1304
M30
%
然后从数控面板调出打印程序,执行打印程序。其中打印程序首先从测量程序调取各支座中心距坐标变量,然后与打印程序中已有的标准值进行计算,计算后的超差值与程序中已有的公差值进行计算,打印计算值。打印计算值的内容包含:测量日期、测量目标、测量方向、测量值、超差值及偏差值。根据计算值和加工余量手动调整各支座孔中心距坐标数值,调整完各支座中心距坐标变量值更改完成。加工时,加工程序直接调用调整后的各支座中心距坐标变量值进行加工。图3、图4所示为现场加工情况。


四、技术改善前后对比
挖掘机动臂、斗杆机加工在线测量技术能够应对各种形式的焊接变形,并保证在加工误差最合理的范围之内。在线测量技术主要计算依赖于加工中心,提高了计算的准确性,降低了人工成本。加工前和加工后的数据以打印的形式保存,打印数据更便于存储和追溯。以我公司21T挖掘机动臂、斗杆为例,原划线工序时间为28min,改善后测量工序时间为5min(见图5)。
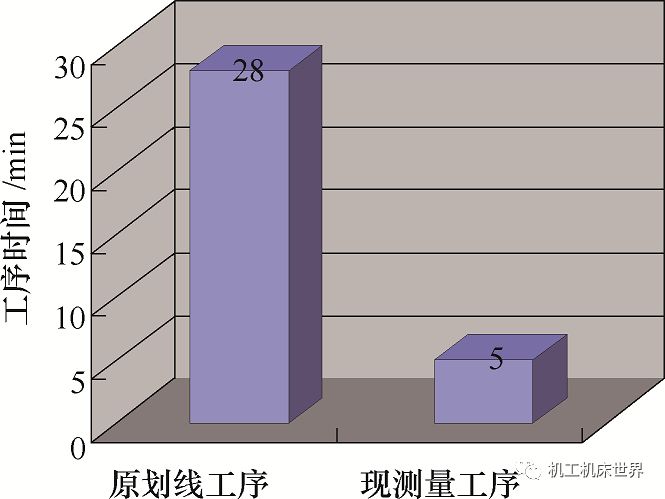