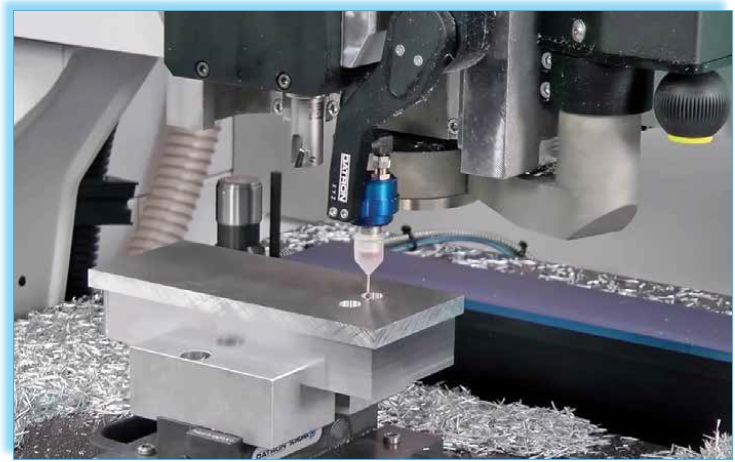
制造商一直在寻找缩短工件加工节拍的有效方法。此外,随着制造业向小型化方向的不断延伸,零部件的尺寸不断减小,更新速度也在不断加快。因此,微型刀具的应用正变得越来越普遍。
传统机床的主轴通常为重型主轴,很难达到较高的转速,其排屑槽也无法达到高效排屑的要求,因此微型刀具在传统机床上很容易发生断裂破坏。
高速加工技术:刀具的尺寸越小所要求的主轴转速也越高,只有这样才能保证加工质量、避免刀具被破坏。高频主轴的转速高达60,000 RPM,是应用微型刀具进行铣削、钻孔、攻丝、雕刻的理想选择。高速加工技术具有转速高、切深小、进给速度快的特点。
在加工过程中,刀具不断地一点点地从工件上切除材料会产生大量的热量,其中40%来自于刀具和工件之间的摩擦生热,20%来自于切屑的变形生热。因此,切屑中承载了大约60%的热量。高速加工技术的目标就是要快速释放切屑中的热量,让切削过程更顺畅。好的加工质量依赖于更快的刀具冷却速度,更小的切削力,更低的震动。
高速加工下的切屑载荷可以降至很低的水平(小于0.005”)。这样的低载荷量意味着刀具和工件之间的压力也会很低。高速切削所产生的热量更少,并且可以用于加工薄壁工件。综上所述,高速加工的刀具冷却速度更快,加工精度更高,切削力更小,质量稳定性更好。
微型刀具的设计优化:简单地将较大直径的刀具按比例缩小成小直径刀具的做法,是无法获得令人满意的进给速率和加工质量的。当刀具直径减小而主轴转速增加时,刀具的结构设计也要作相应的变化。传统的嵌入式结构已经不能满足微型刀具的应用需要了。主要的矛盾点在于高转速,而不在于小直径。主轴转速越高要求刀具的动平衡性能更好,排屑能力更强,这样才能避免切屑烧结的发生。也就是说微型刀具的高效切削有赖于刀具的结构优化,这种优化就是为了解决高转速的动平衡问题。如果微型刀具的几何结构适当,主轴转速够高,冷却液选择合理,则完全可以省掉去毛刺和除油垢等二次加工步骤。
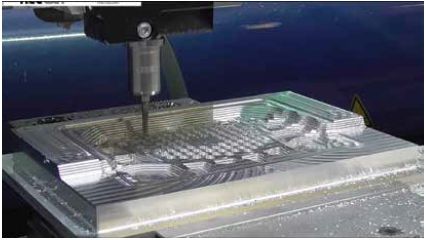
在设计机床时,目前有两个研发方向。第一,可以选择大功率电机和重型主轴来提供高切削力和扭矩。第二,可以使用低切削力,高速主轴来配合微型刀具实现轻型加工。当然这两个发展方向的机床功能都可以是多元化的,例如铣削、钻削、锥度加工等。如果加工效率和质量对您来说是同等重要的,并且要同时满足大型工件和小型工件的加工需求,那么两类机床的引进都是必要的,需要将它们合理配置到您的厂房中。
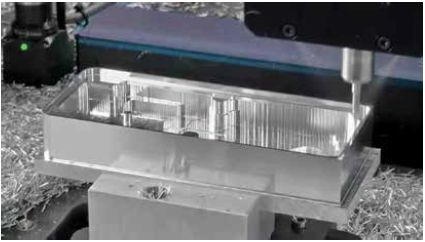
这里举两个高速加工的应用实例。第一个是在Datron机床上进行的,工件材料为6061铝,刀具为6.35mm(1/4英寸)的单刃铣刀,切深为3.175mm(1/8英寸),主轴转速45,000RPM,乙醇冷却,进料速率为6.35m(250英寸)/ min。
第二个实例,仍然是在Datron机床上进行,工件为厚度为3.175mm(1/8英寸)的6061铝制薄板,刀具为低螺旋角的3.175mm(1/8英寸)双刃高速铣刀(HSC +),主轴转速50,000RPM,乙醇冷却,进料速率为5.08m(200英寸)/ min。
高速加工要遵循一定的经验法则。首先,要避免主轴过热,过热会增加磨损、缩短主轴寿命。切深不能超过刀具直径的一半,采用小的切深但高的进给速率。最后,排屑速度也要跟着加快。
结论
总之,选择合适的刀具完成合适加工任务。低转速、高切削力的传统机床无法达到微型刀具高速加工的生产效率。只有引进新的专业机床设备,才能和这种高效的加工方式相匹配,当然它的效果也是令人惊艳的,完全满足复杂零件高效率、高质量加工的需要。