1 L/D=10~20,属于一般深孔。常在钻床或车床上用接长麻花钻孔加工。
2 L/D=20~30,属于中等深孔。常在车床上加工。
3 L/D=30~100,属于特殊孔深。必须使用深孔钻在深孔钻床或专用设备上加工。
2. 切削热不易传出。
3.排屑较困难,如遇切削阻塞则会引起钻头损坏。
4.因钻杆长、刚性差、易振动,会导致孔轴线偏斜,影响到加工精度及生产效率。
深孔钻的类型、使用范围及工作原理,深孔钻按排屑方式分为外派屑和内排屑2种,外排屑有枪钻、整体合金孔钻(可分为有冷却和无冷却孔2种):内排屑又分为BTA深孔钻、喷吸钻和DF系统深孔钻3种。(下面我们来介绍下曲轴油孔工艺)
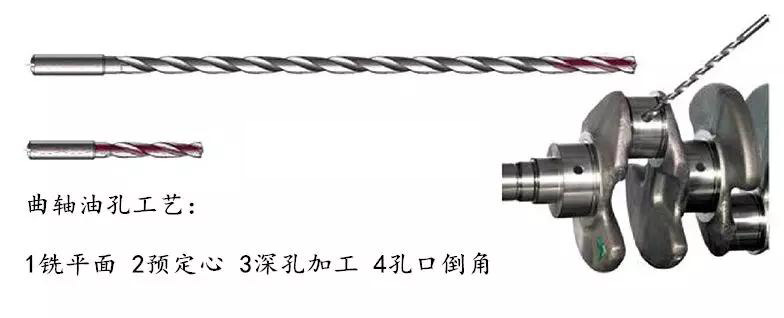
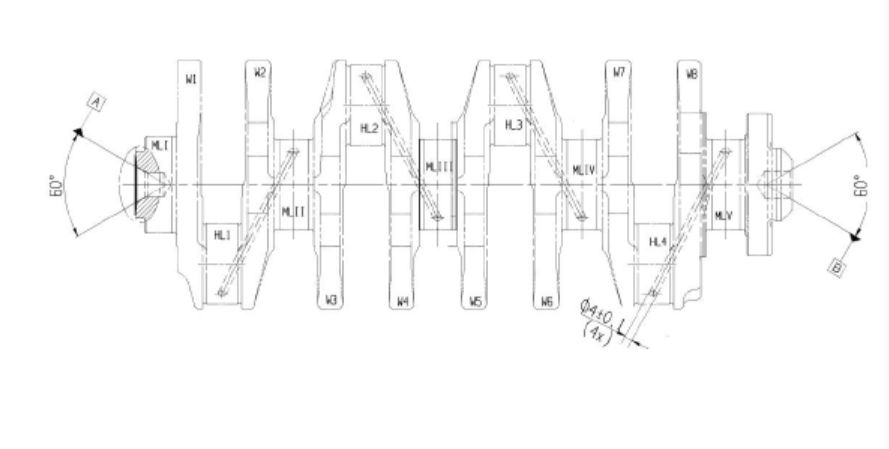
第二步:选择引导钻在连杆或主轴上钻入1.5D-2D的孔深(为后序深孔钻提供良好的导向和预钻准备)。
第三步:选择深孔钻头在已有的孔径上钻通该孔径。
第四步:(主轴/连杆颈)孔口倒角,去除孔口毛刺。
PS:曲轴油孔工艺一般分为两种类型,
1、交叉孔:连杆油孔和主轴油孔相互交叉。
(加工有难度)
2、直通孔:连杆有油孔,主轴无油孔。
上面描述的油孔工艺是很多工厂采用的普遍方式,也有的工厂把第一步和第二步合并了,用平底钻当做引导钻的方式进行预定心(这里不建议工厂采用这种形式),貌似加工的效率提高了,其实后面的刀具维护成本会增加,请注意。(有需要油孔加工程序的可以联系小编我,提供程序供您研究)
- 一般平底钻和引导孔的长短很接近,在更换刀具的时候请操作者要看清楚,否则容易发生撞刀事件。
- 倒角钻在加工孔口倒角的时候,孔口倒角的大小会有差别,一般是新刀换刀后,一般是刀具磨损剧烈情况,(换刀/程序中修改参数可以改正过来)。
- MQL流量变小,这个会导致深孔钻断裂,产品报废,(点检可以发现这类问题,油品日常的消耗也可以发现)。
- 修磨回来的深孔钻在装刀前,要看内冷孔是否有阻塞现象。
1.深孔加工操作要点
主轴和刀具导向套、刀杆支撑套、工件支撑套等中心线的同轴度应符合要求;切削液系统应畅通正常;工件的加工端面上不应有中心孔,并避免在斜面上钻孔;切削形状应保持正常,避免生成直带状切削;采用较高速度加工通孔,当钻头即将钻透时,应降速或停机以防损坏钻头。
2.深孔加工切削液
深孔加工过程中会产生大量的切削热,并不易扩散,需要供给充足的切削液润滑冷却刀具。一般选用1:100的乳化液或极压乳化液,需要较高加工精度和表面质量或加工韧性材料时,选用极压乳化液或高浓度极压乳化液,切削油的运动粘度通常选用(40)10~20 cm²/s,切削液流速为15~18 m/s ;加工直径较小时选用粘度低的切削油;要求精度高的深孔加工,可选用切削油配比为40%煤油+20%氯化石蜡。
切削液的压力和流量与孔径及加工方式有着密切的关系。
外排屑深孔钻切削液的压力与流量
孔径/mm
压力/Mpa
流量/(L/min)
4-10
2.5-6
8-20
10-15
2-5
20-30
15-20
1.5-4.5
30-40
25-20
1.5-4
40-50
25-30
1.5-3
50-60
内排屑深孔钻切削液的压力与流量
孔径/mm
压力/Mpa
流量/(L/min)
8-15
5-6.5
20-50
15-25
4-5.5
50-70
25-35
3-4.5
70-100
35-45
2.5-4.5
100-125
45-80
2-3
125-200
3.使用深孔钻注意事项
折断-开始加工时
原因
排除措施
设
备
原
因
检查进给机构(是否进给太快);检查工件是否夹紧或有松动;防止偏摆,套筒安装是否正确.
钻
头
原
因
修磨是否有问题.
套
筒
端
面
原
因
检查是否漏油和有没有切削液卡在端面处.
折断-钻削时
原因
排除措施
设
备
原
因
检查进给机构(是否进给太快);检查工件是否夹紧或有松动;防止偏摆,套筒安装是否正确.
刀
具
损
伤
大
参考刀具寿命部分.
折断-钻通时
原因
排除措施
进
给
速
度
退刀时轴向推力减小,进给速度太快,降低进给速度.
折断-退刀时
原因
排除措施
被加
工工
件形
状
检查快钻通部分的孔是否钻歪.
刀具寿命-寿命短
原因
排除措施
钻削
条件
不合
理
边框/背景是设置在单元格上的.
设
备
原
因
主轴偏摆是否过大,检查主轴和导向套是否同心,导向套和钻柄的间隙是否太大;防止偏摆,套筒的安装是否正确.
刀
具
原
因
钻尖角和导向块选择是否正确;钻头长度是否比需要长度太多;重磨是否符合要求(砂轮粒度是否太粗,崩刃未磨掉).
切
削
液
原
因
切削液的选择是否正确(添加剂,粘度等);切削液的过渡是否良好;油温太高时应增加邮箱容积.
被
加
工
材
料
材质性质是否均匀.
加工精度-表面粗糙度
原因
排除措施
切削
条件
不正
确
降低进给速度.
设
备
问
题
检查主轴偏摆,进给速度的均匀性,导向套精度,工件是否夹紧.
刀
具
问
题
钻头是否夹持是否松动.
切
削
液
问
题
切削液的选择是否正确,选择适当的切削液;充分过渡切削液.
加工精度-圆柱度/圆度/扩孔超差
原因
排除措施
切削
条件
不正
确
选择适当的进给速度.
设
备
问
题
提高导向套精度和导向套与主轴的同心度.
刀
具
问
题
选择适当的钻尖形状,角度.
切
削
液
问
题
选择适当的切削液.
加工精度-弯曲
原因
排除措施
设
备
问
题
提高导向套精度和导向套与主轴的同心度;稳定地夹紧被加工件.
刀
具
问
题
选择合适的钻尖形状,角度和导向块.
设
备
问
题
检查表面是否有切屑,砂眼;检查表面是否有斜度,将表面加工平整.
被加
工工
件材
料问
题
检查表面是否有切屑,砂眼;检查表面是否有斜度,将表面加工平整.
切屑处理-切屑堵塞/缠屑
原因
排除措施
切削
液压
力低
正确选择切削液压力.
切削
液流
量小
正确选择切削液流量;检查切削液粘度是都太大,降低粘度.
切屑
形态
不理
想
切屑很硬时,降低进给速度;正确选择钻尖形状,角度.
设
备
问
题
增大容屑空间.
丝
状
切
屑
提供进给速度,检查钻尖切削刃转角处磨损是否太大;检查钻尖切削刃转角处切削刃是否崩刃;重磨时的砂轮粒度是否太粗;钻中心孔时产生丝状切屑,提高切削液压力,降低进给量.
锯
齿
状
切
屑
检查钻尖或靠近钻尖处的切削刃是否崩刃.