一、刀具半径补偿的基本概念
1.为什么是刀具半径补偿?
数控机床在轮廓加工过程中,它所控制的是刀具中心的轨迹,而用户编程时则是按零件轮廓编制的,因而为了加工所需的零件,在进行轮廓加工时,刀具中心必须偏移一个刀具半径值。
数控装置根据零件轮廓编制的程序和预先设定的刀具半径参数,能实时自动生成刀具中心轨迹的功能称为刀具半径补偿功能。
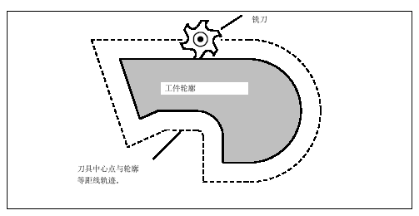
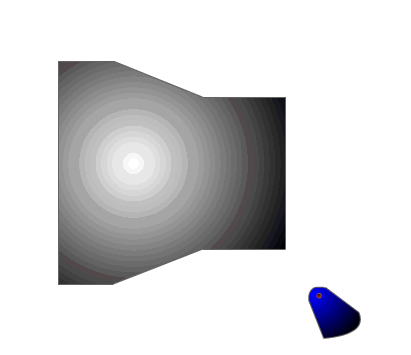
2.刀具半径补偿功能的主要用途
① 实现根据编程轨迹对刀具中心轨迹的控制。
② 实现刀具半径误差补偿。
③ 减少粗、精加工程序编制的工作量。
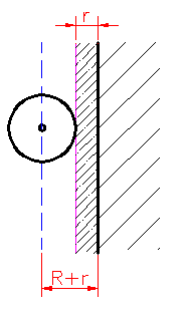

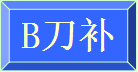
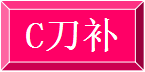
相邻两段轮廓的刀具中心轨迹之间用圆弧连接。 相邻两段轮廓的刀具中心轨迹之间用直线连接。
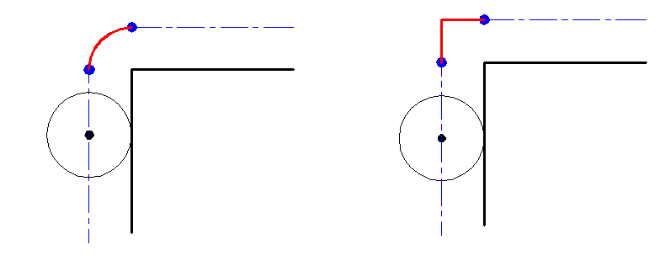
优点:
√算法简单,容易实现
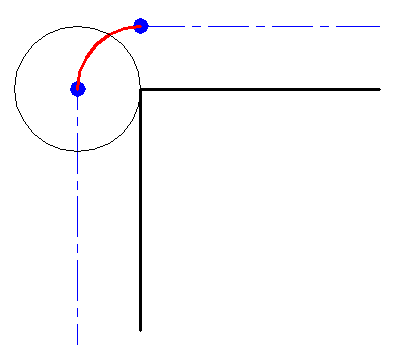
缺点:
×在外轮廓尖角加工时,由于轮廓尖角处,始终处于切削状态,尖角加工的工艺性差。
×在内轮廓尖角加工时,编程人员必须在零件轮廓中插入一个半径大于刀具半径的圆弧,这样才能避免产生过切。
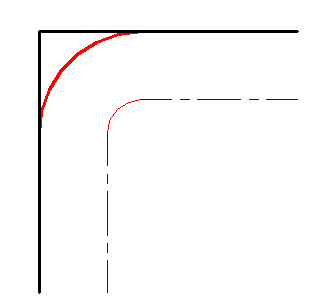
(2)C刀补
由数控系统根据和实际轮廓完全一样的编程轨迹,直接算出相邻刀具中心轨迹的交点,然后再对原来的中心轨迹作伸长或缩短的修正。
√尖角性好。
√内轮廓加工时,以免产生过切。
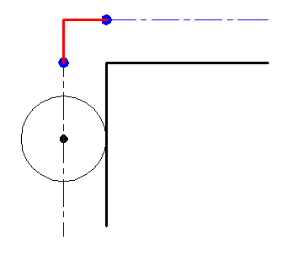

(3)B刀补与C刀补比较
区别:B刀补法在确定刀具中心轨迹时,一次处理一段轨迹,采用的是读一段,算一段,再走一段的处理方法。这样,就无法预计到由于刀具半径补偿所造成的下一段加工轨迹对本段加工轨迹的影响。
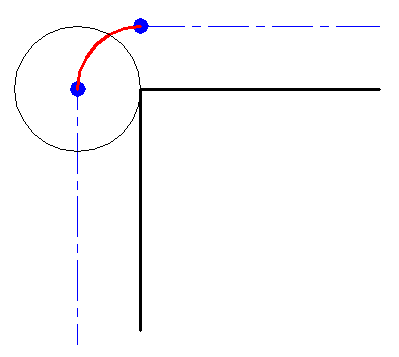
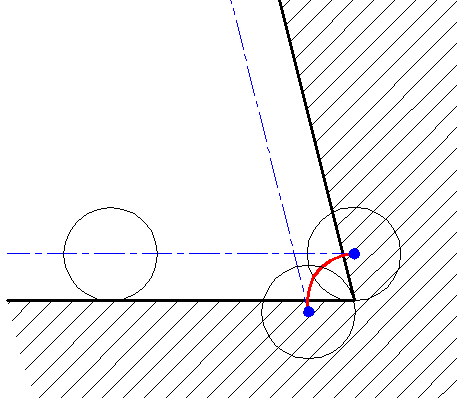
区别:C刀补采用的方法是一次对两段进行处理,即先预处理本段,然后根据下一段的方向来确定其刀具中心轨迹的段间过渡状态,从而便完成了本段的刀补运算处理。
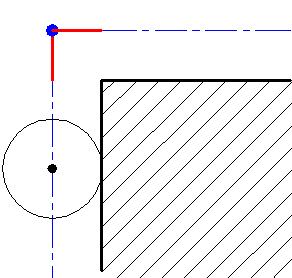
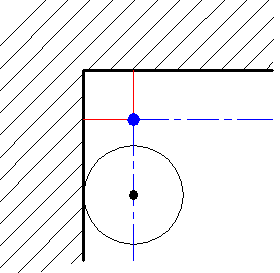
二、刀具半径补偿的工作原理
1.刀具半径补偿的工作过程
刀具半径补偿执行的过程一般可分为三步:
(1)刀补建立
(2)刀补进行
(3)刀补撤销
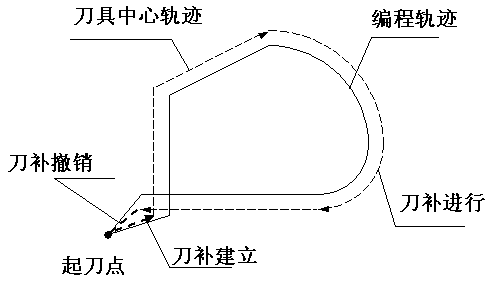
使用刀具半径补偿功能注意事项
1、必须在运动中建立和取消刀补,G41/G42没有使刀具运动的功能;
2、不能在圆弧程序段上建立和取消刀补;刀具半径补偿功能只能在轮廓的插补平面内生效,而在除插补平面外的其它坐标轴上不起作用;
3、在刀补执行过程中,不能有连续两段指令为非插补平面运动的指令,否则产生过切。
二.C刀补偿的转接形式和过渡方式
(1)转接形式
在一般的CNC装置中,均有圆弧和直线插补两种功能。由于C刀补采用直线过渡,实际加工过程中,随着前后两编程轨迹的线型不同,也会产生不同的转接情况:
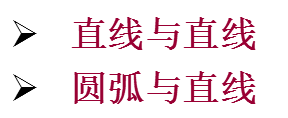
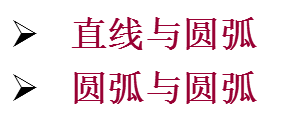
(2)过渡方式
矢量夹角α 指两编程轨迹在交点处非加工侧(工件侧)的夹角α
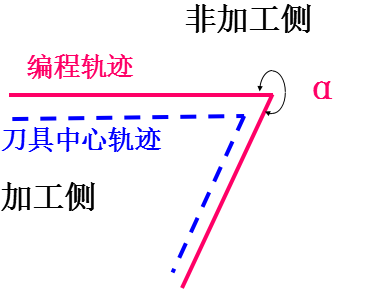

根据两段程序轨迹的矢量夹角α和刀补方向的不同,又有以下几种转接过渡方式:
缩短型:矢量夹角180°≤α<360°
刀具中心轨迹短于编程轨迹的过渡方式。
伸长型:矢量夹角90°≤α<180°
刀具中心轨迹长于编程轨迹的过渡方式。
插入型:矢量夹角α<90°
在两段刀具中心轨迹之间插入一段直线的过渡方式。
缩短型:
矢量夹角180°≤α<360°
刀具中心轨迹短于编程轨迹的过渡方式。
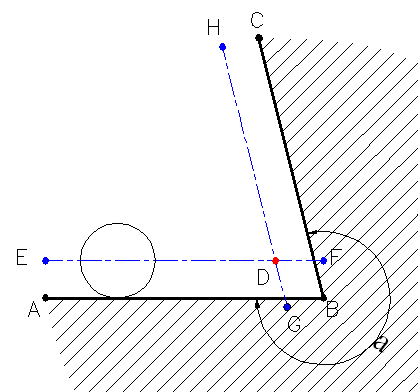
矢量夹角90°≤α<180°
刀具中心轨迹长于编程轨迹的过渡方式。
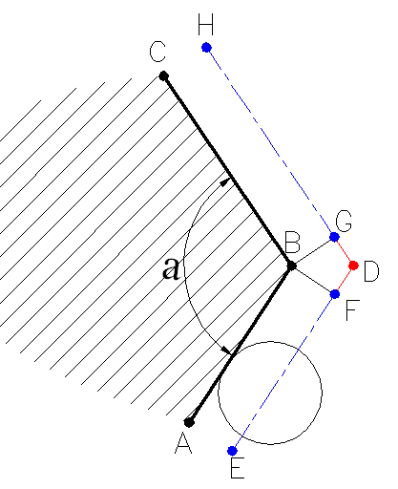
插入型:
矢量夹角α<90°
在两段刀具中心轨迹之间插入一段直线的过渡方式。
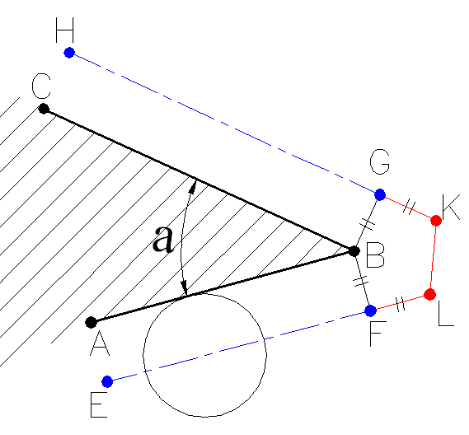
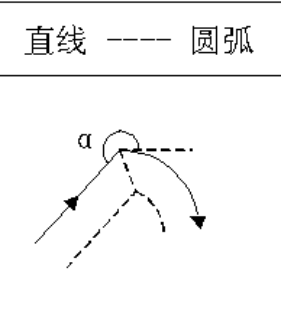
缩短型:180°≤α<360°

伸长型:90°≤α<180°
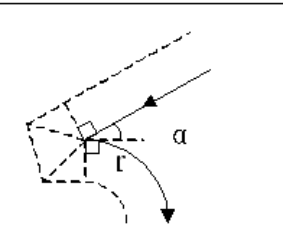
插入型:α<90°
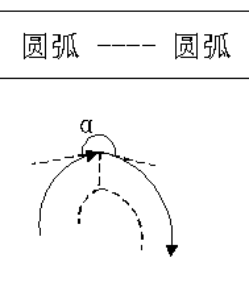
缩短型:180°≤α<360°
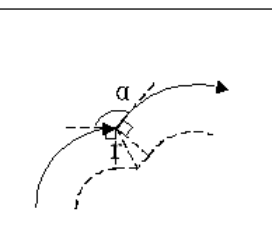
伸长型:90°≤α<180°
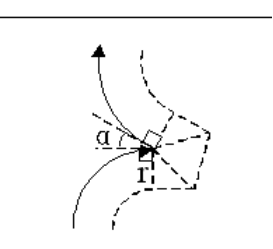
插入型:α<90°
三、加工过程中的过切判别
当被加工的轮廓是直线段时,若刀具半径选用过大,就将产生过削现象。
当读入编程轨迹CD时,就要对上段刀具中心轨迹B’C’进行修正,确定刀具中心应从B′点移到C′点。显然,这时必将产生如图阴影部分所示的过切削。
1.直线加工时的过切判别方法
可以通过编程矢量与其相对应的修正矢量的标量积的正负进行判别。在上图中,BC为编程矢量, 为BC对应的修正矢量,α为它们之间的夹角。则:标量积
显然,当
(即90o<α<270o)时,刀具就要背向编程轨迹移动,造成过切削。上图中α=180o,所以必定产生过切削。
2.圆弧加工时的过切削判别
在内轮廓圆弧加工(圆弧加工的命令为 G41G03 或G42G02)时,若选用的刀具半径rD过大,超过了所需加工的圆弧半径R,那么就会产生过切削。
过切削现象都发生在过渡形式为缩短型的情况下,因而可以根据这一原则,来判断发生过切削的条件,并据此设计过切削判别程序。
设刀具开始位置距工件表面上方50mm,切削深度为8。
N01 G91 G41 G00 X20.0 Y10.0
N02 Z-48.0 ;
N03 G01 Z-10.0 F200 ;
N04 Y30.0 ;
N05 X30.0 ;
N06 Y-20.0 ;
N07 X-40.0 ;
N08 G00 Z58.0 ;
N09 G40 X-10.0 Y-20.0 ;
N10 M02 ;
N05 G91 X60.0 ;
N06 M08 ;
N07 M09 ;
N08 Y-15.0 ;
N09 X40 .0 ;
当N05程序段加工AB轮廓,同时读入N06和N07两段,因这两段为辅助功能指令,作不出沿BC轮廓垂直矢量,而直接到达S点,造成过切现象。