在切削过程中,数控刀具几何参数的不同组合形成不同的切削形态。直接影响切削过程的稳定性和表面质量。理想状态下,采用圆弧刃金刚石刀具进行超精密车削加工软金属时,在工件加工表面形成轮廓峰和轮廓谷,它们之间的距离,被称为理论粗糙度,其大小等于f2/8R(f为进给量,R为刀具圆弧半径)。
在超精密切削塑性金属时,主切削刃和前刀面的主要任务是去除金属,切削层在前刀面的挤压作用下发生剪切滑移和塑性变形,然后形成切屑沿前刀面流出。前刀面的形状直 接影响塑性变形的程度、切屑的卷曲形式和切屑刀具之间的摩擦特性,并直接对切削力、切削温度、切屑的折断方式和加工表面质量造成显著影响。主切削刃是前刀 面和后刀面的交线。实际上前刀面和后刀面的交线不可能为理想直线,而是一微观交接的曲线。该曲线的形状可以近似用与其在不同位置的法平面相交成交线的平均 曲率半径来反映,称其为刃口半径ρ。切削时刃前区的应力状态十分复杂,应力集中造成金属中位错集中,导致金属产生塑性变形和滑移分离,一部分金属成为切屑 沿前刀面流出,另一部分金属经后刀面熨压留在已加工表面。因为两部分金属运动方向不同,必然使刀具刃口前金属呈拉伸状态,拉应力使刃前区金属的抗剪能力下 降,在刀刃的直接作用下,金属产生滑移分离。刃口半径越小,应力越集中,变形越容易,切削力越小,加工表面质量越好。也就是说刃口半径对切削过程有较大影 响,同时对切削力、切削温度和切屑变形系数都有不同程度的影响。因此,提高刀具的锋锐程度,可减小刀具对金属的挤压力,使金属的变形程度降低,减缓金属的 冷作硬化,有助于提高切削过程的稳定性,改善加工表面质量和延长刀具的使用寿命。
2 最小切削厚度对表面粗糙度的影响
除了机床本身的性能以外,使用刀具切削刃有效地切除工件材料时,最小切削厚度(MTC)的可控性和重复性是影响加工精度的主要因素。MTC 不仅可以反映切削刃的纳米级微观结构,还可以反映出刀具和工件材料之间的相互作用状态。最小切削厚度被定义为能够从工件材料上有效地去除金属的最小厚度。 切削厚度越小,工件材料抵抗塑性变形的能力越强,刀具和材料原子之间的相互作用力越弱。当金刚石刀具刃口半径为几个纳米的特定切削环境下,最终可达到的加 工精度与最小切削厚度为同一个数量级。日本学者在高稳定的机床上使用特制的金刚石刀具切削单晶铜,获得了非常微细的切屑,并使最小切削厚度可以达 到$%&。最小切削厚度这个变量随着刀具的几何形状和切削条件的不同而变化。美国和日本有关专家通过实验研究发现:金刚石刀具的刃口半径r对最小 切削厚度有显著的影响,当车削铝合金的时候,最小切削厚度大约为所采用刀具刃口半径的0.3~0.6 倍,这个比值随着被加工材料和切削条件(如进给量和刀具的圆弧半径)的不同而略有差异。
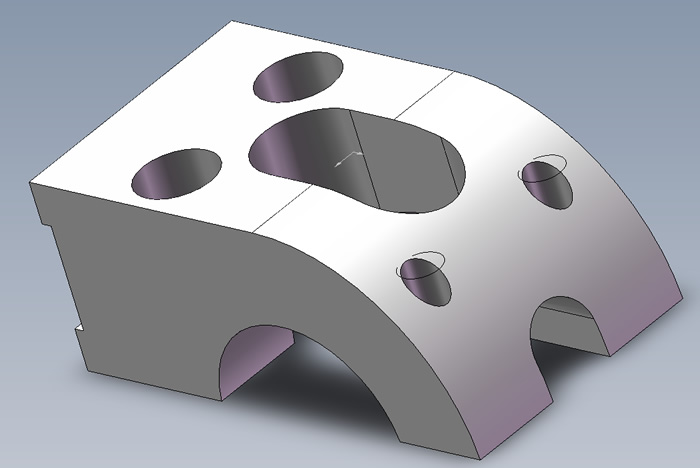
3 金属变形对表面粗糙度的影响
金属切削加工过程非常复杂,加工后形成的表面粗糙度与工件的材料、刀具的几何形状、润滑方法以及选用的切削深度密切相关。剪切、滑移和断裂被认为是影响切屑形成的几个主要因素。超精密切削时只要有切屑产生,就可以把该过程模型化为材料沿着与水平面倾斜一定角度的平面被刀具剪切的过程,在已加工表面上形成 的峰、谷高度随刀具刃口锋锐轮廓的变化而变化。
另外,工件材料对金刚石车削加工表面粗糙度有显著的影响,在一般车削加工中经常 忽略材料晶体微观结构的影响,而金刚石车削中材料对表面粗糙度的影响却不容忽视。例如:某种材料的弹性模量主要依赖于单晶体的晶向,虽然铜、铝同样是软金 属,但它们的硬度却有较大差异。在同样条件下切削上述两种金属时,切削状态不同,产生切削力的大小也会有所不同。另外,被加工材料的纯度、材质是否均匀以 及晶体的晶向各异性都会对加工表面质量产生重要影响。
4 切削用量对表面粗糙度的影响
在 113m/min≤V≤314m/min,1.8µm/r≤f≤5.0µm/r,1.50µm≤ap≤6.00µm的条件下,建立金刚石车刀车削铝合金表 面粗糙度的预测模型,(V:切削速度,f:进给量,ap:背吃刀量),从中可以看出各种切削参数对表面粗糙度值的影响。
在上述 的条件下,从预测模型可反映出:随着切削速度的增加,表面粗糙度值略微减小,这种变化主要受机床动态特性的影响。当 f=5.0µm/r,ap=6.00µm时,表面粗糙度的变化范围仅为2nm左右,因此说切削速度对表面粗糙度基本无影响。金刚石车削铜合金时也能够得到 同样的结论。当切削速度为314m/min、进给量为5µm/r时,背吃刀量小于6µm时,对加工表面粗糙度基本无影响。 当切削速度为314m/min、背吃刀量为6µm时,可知小进给量可得到小的表面粗糙度值。但是由于最小切削厚度的存在,实测的表面粗糙度值往往要比理论 粗糙度值大几倍。
5 振动对表面粗糙度的影响
尽管超精密车床具有很高的刚度,但振动仍然是影响表面 粗糙度的主要因素之一。超精密机床通常都有很高的固有频率,在超精密加工过程中,实际的工艺系统是一个非常复杂的振动系统,系统中的振动使工件与刀具之间 的相对位置发生了微幅变动,最终使工件表面粗糙度增大、表面质量降低。有关学者通过研究发现:机床主轴的振动、导轨的振动以及刀具的振动都具有高频率、小 振幅的特征,积屑瘤、外界干扰、机床刚性不足以及高速旋转部件不平衡也会引起切削振动,最终导致加工表面微观特征的改变。