机床夹具设计实例教程
1)组合夹具虚拟设计实例
具体应用步骤有:
①以零件实体模型作为设计依据
②按设计需要选用支撑组件、压紧组件、基础组件、定位组件、导向组件等元件、组件。
*元件、组件不带知识库的可以从标准件、组件树上直接下载。
*元件、组件带知识库的,通过组件设计推理,进行组件、元件的推理和系列尺寸驱动,并下载到工作区,进行装配。
③组件和元件之间的装配。对于已经下载的各类元件和组件,使用三维CAD平台装配功能进行装配,并输出结果,完成整个组合夹具的设计。组合夹具其装配示例见图12-22,SolidWrorks平台下的增强装配实例见图12-23.
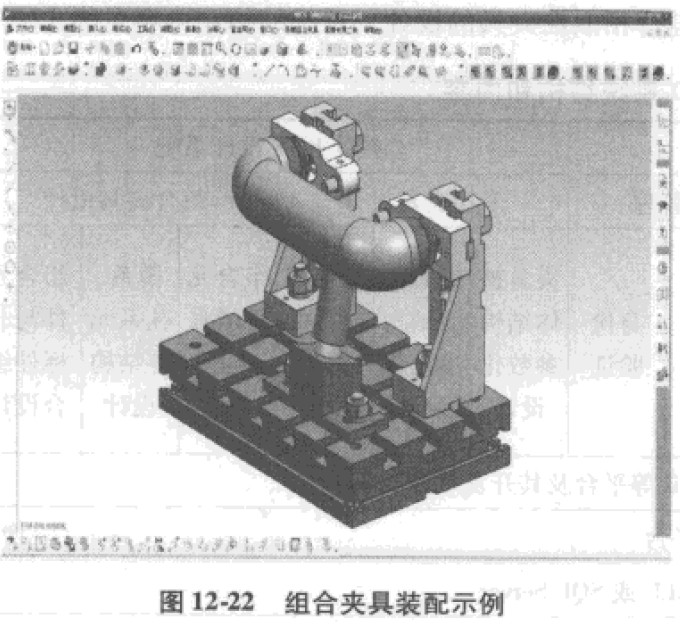
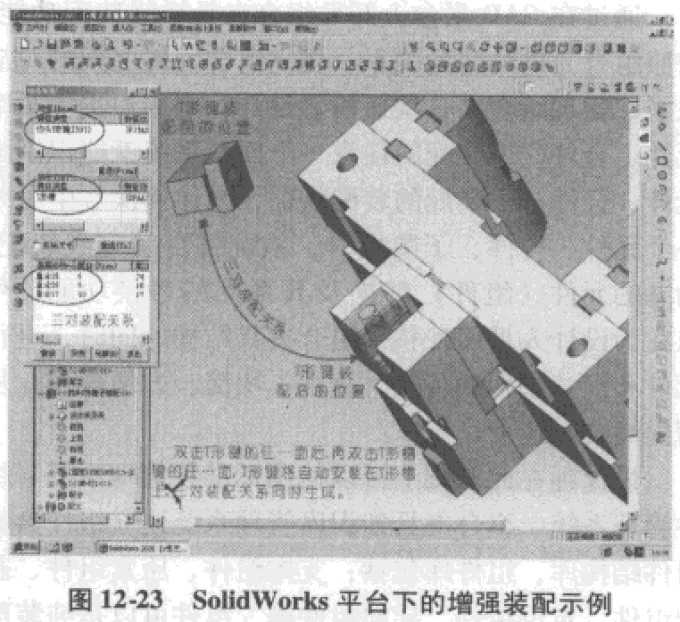
2)专用夹具设计实例
具体设计步骤
①根据被加工零件的尺寸参数及其形状,在基础版库中选择可用基础版或进行基础版建模;连杆被加工零件见图12-24,基础版见图12-25.
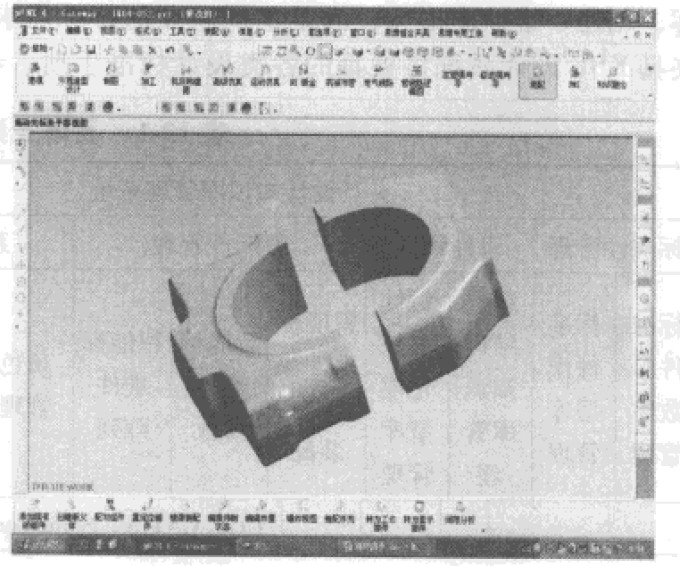
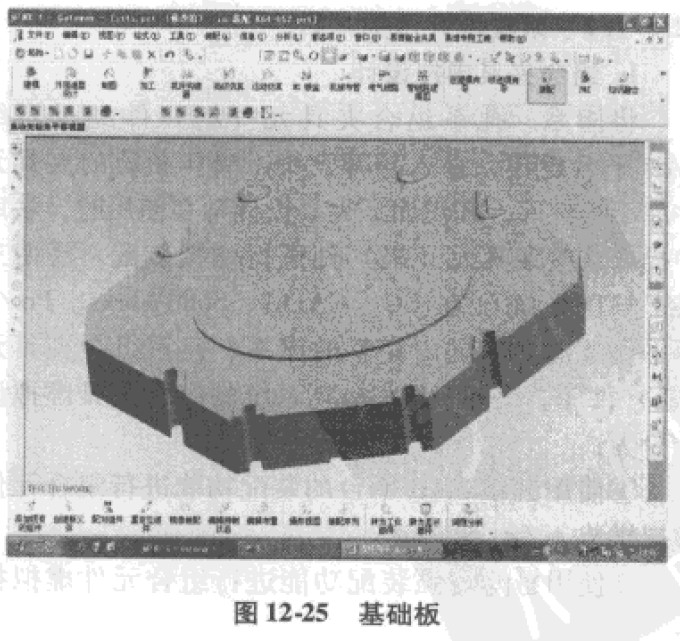
②智能件打孔装配加快专用夹其设计。将标准件紧固螺钉、定位销、螺栓、档销等制作成具有装配属性的智能件,这些智能件具有打孔、装配一次性完成功能,并可实现多层板的打孔及各层板的间隙设置。定位销智能件在打孔装配操作后,还具有阵列、删除、修改等功能,如若智能件规格不台适,还可直接进行足寸系列替换,大大提高了专用夹具的工作效率。挡销智能件见图12-26,智能件打孔装配及阵列见图12-27。
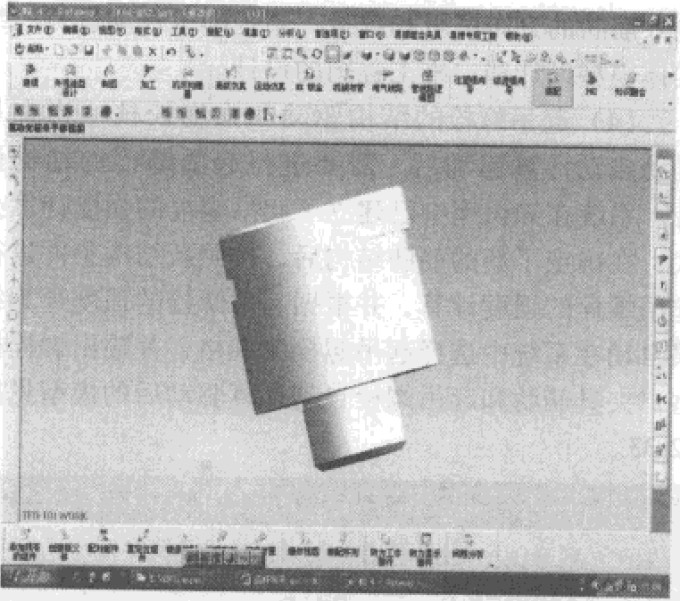
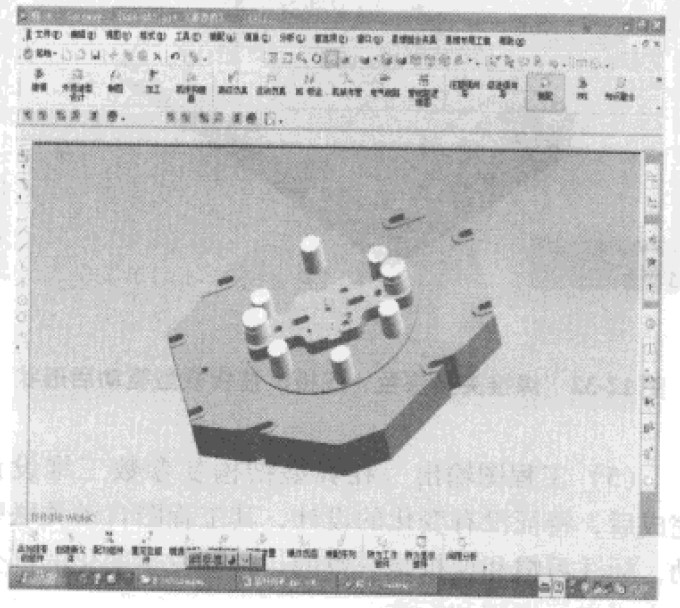
③组件知识库推理及打孔装配。建立夹具组件知识库和智能件,通过采集相关信息,对组件进行知识库参数化驱动,并实现组件打孔装配,阵列,提高组件设计效率。压板组件打孔快速装配见图12-28,压板组件打孔阵列见图12-29。
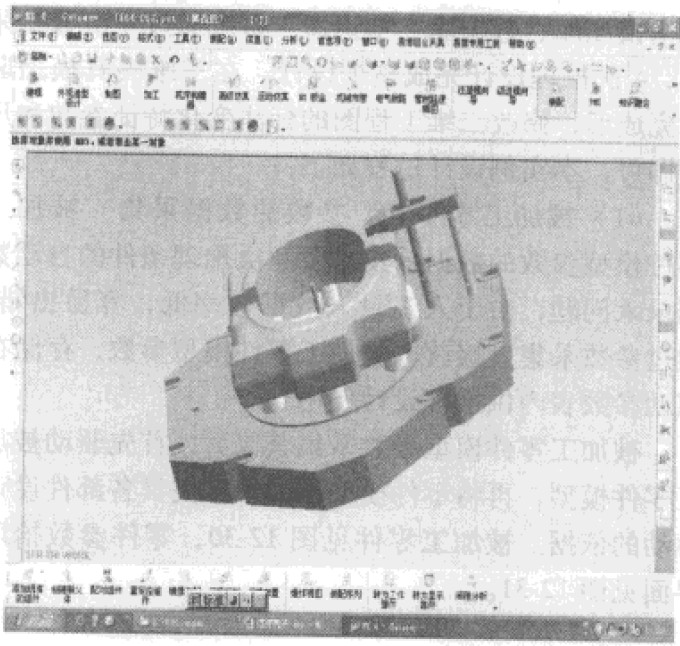
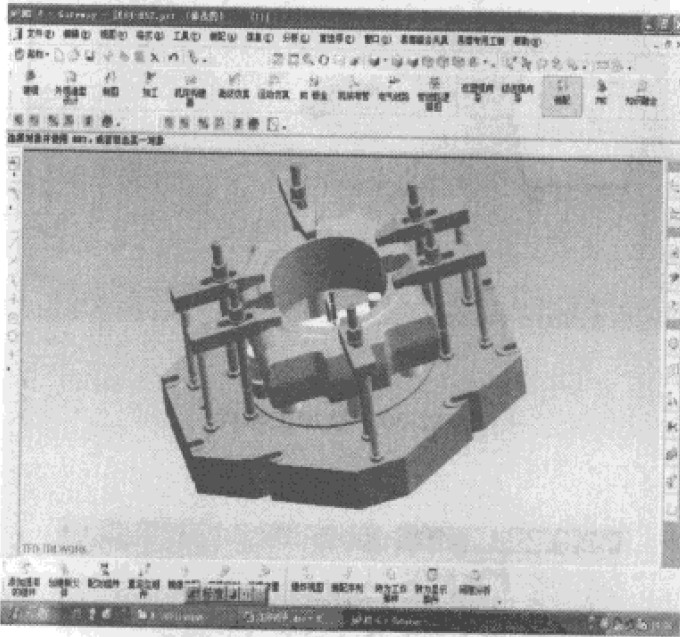
3)夹具典型整体结构设计实例
当夹具具有整体结构重用价值时,系统通过建立夹具典型整体结构参数化模型库、知识库,实现夹具变结构快速设计,在设计环节中如果遇到一些强度计算问题,在建立知识库推理时可以将相应的公式计算(含有限元分析计算结果)整理入库,当再次使用时通过系统进行推理计算以满足快速设计的需要。以下结合某厂焊接夹具设计为例,简述典型整体结构设计过程。通过前期对焊接夹具典型结构的实体模型、设计经验、计算公式、二维工程图等数据、图形的总结整理后.已经建立该类零件的焊接夹具典型结构模型库、数据库、知识库。系统通过4次数据采集,4次推理设计完成整个设计。在三维夹具模型驱动完成后,修改二维工程图的标注变化特征参数和尺寸即可。
本实例设计过程如下:
①被加工零件模型参数的数据采集被加工零件模型参数的数据采集主要解决推理条件的自动数据录入问题,由于人工录人数据效率低,容易出错。通过参数采集直接获取被加工零件模型参数,存储在驱动参数表内供推理设计使用。被加工零件模型参数采集获取后,首先驱动被加工零件模型,再将零件模型作为焊接夹具各部件设计驱动的依据。被加工零件见图l2-30,零件参数拾取界面见图12-31。
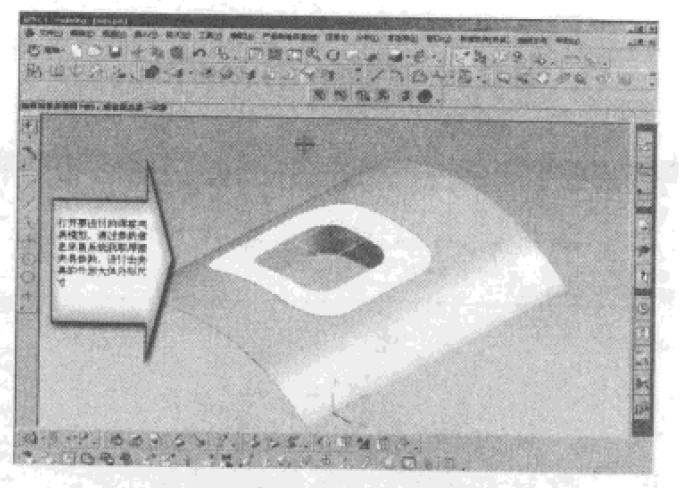

②驱动法兰、底板、盖板零件模型由被加工零件模型的驱动结果作为焊接夹具法兰、底板、盖极零件模型驱动条件,在知识库中自动进行推理驱动,焊接夹具法兰,底板、盖板模型驱动后形状见图12-32
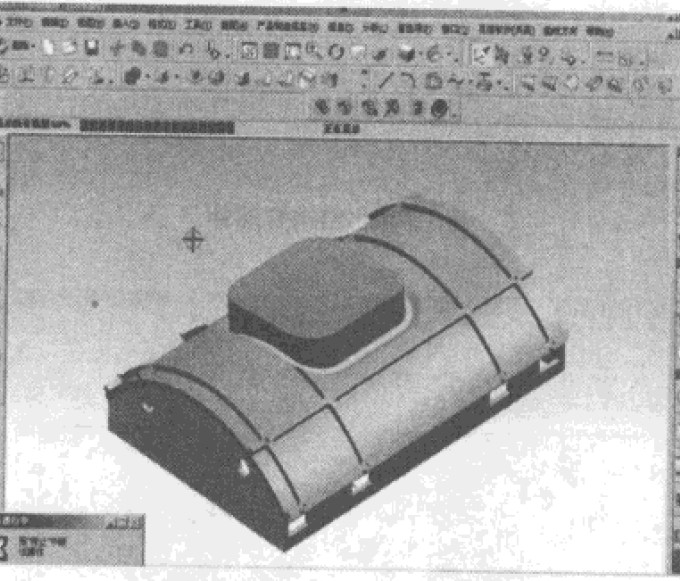
③筋肋自动计算驱动
焊接夹具的筋肋设计是一项非常繁琐的设计工作,设计员需要反复计算、画图,如果一次计算不合理或因其它原因变化还需反复修改,工作量大。本设计在知识库中建立了推理规则,将筋肋设计经验和算法存入知识库,设计时只需输入筋肋的分布区域和数量,系统即可自动进行三维实体模型设计和二维工程图的设计。
④起吊螺栓的结构驱动和强度校核
当夹具筋肋自动计算驱动后,需要进行起吊螺栓的结构设计。系统在知识库中已建立了起吊螺栓的强度计算公式,在确定了新的筋肋结构后,按照新结构条件进行起吊螺栓的强度计算,并根据起吊螺栓的强度计算结果自动在系统中选择起吊螺栓的规格,井输出螺栓模
型.夹具筋肋和起吊螺栓自动计算骄动后的模型见图12-33。
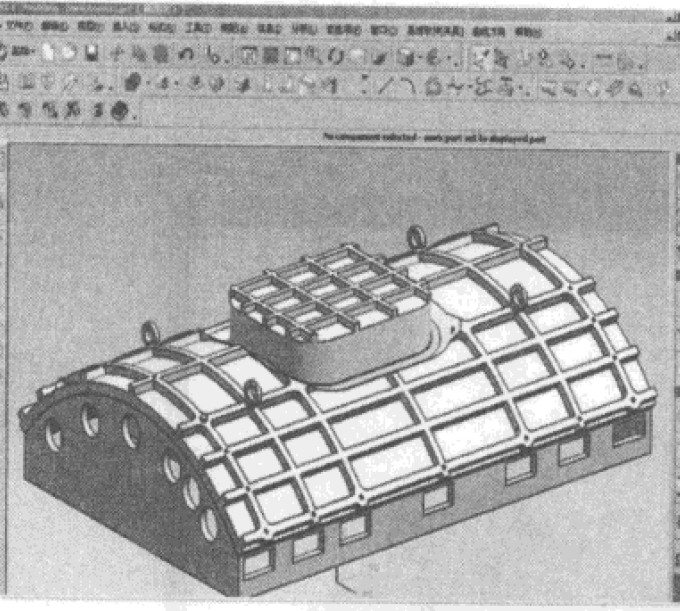
⑤工程图输出
在典型结构变参数三维设计完成后,特征没有变化的设计,其工程图自动关联驱动,标注习惯和模板是一致的,特征发生变化的部分由人工进行调整和标注。
钻夹具的设计实例
图2-2-20所示为杠杆类零件图样。图2-2-21所示为本零件工序图。
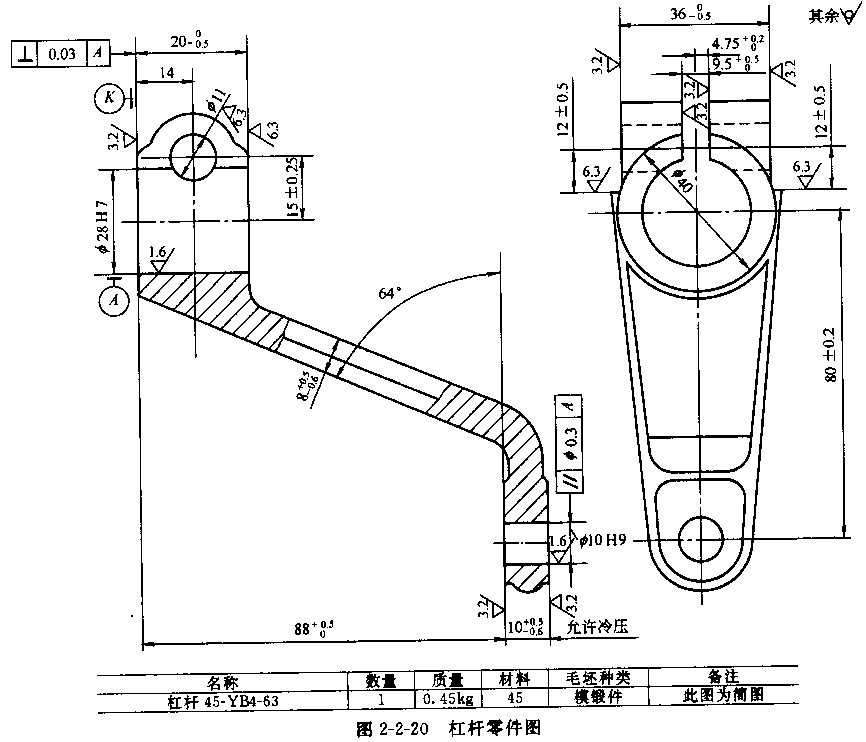
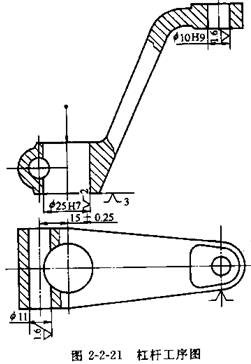
1.零件本工序的加工要求分析
①钻、扩、铰φ10H9孔及φ11孔。
②φ10H9孔与φ28H7孔的距离为(80±0. 2)mm;平行度为0.3mm。
③φ11孔与φ28H7孔的距离为(15±0. 25)mm。
④φ11孔与端面K距离为14mm。
本工序前已加工的表面如下。
①φ28H7孔及两端面。
②φ10H9两端面。
本工序使用机床为Z5125立钻,刀具为通用标准工具。
2.确定夹具类型
本工序所加工两孔(φ10H9和φ11),位于互成90°的两平面内,孔径不大,工件质量较小、轮廓尺寸以及生产量不是很大,因此采用翻转式钻模。
3.拟定定位方案和选择定位元件
(1)定位方案。根据工件结构特点,其定位方案如下。
①以φ28H7孔及一组合面(端面K和φ10H9一端面组合而成)为定位面,以φ10H9孔端外缘毛坯面一侧为防转定位面,限制六个自由度。这一定位方案,由于尺寸 mm公差大,定位不可靠,会引起较大的定位误差。如图2-2-22(a)所示。
②以孔φ28H7孔及端面K定位,以φ11孔外缘毛坯一侧为防转定位面,限制工件六个自由度。为增加刚性,在φ10H9的端面增设一辅助支承,如图2-2-22 (b)所示。
比较上述两种定位方案,初步确定选用图2-2-22(b)所示的方案。
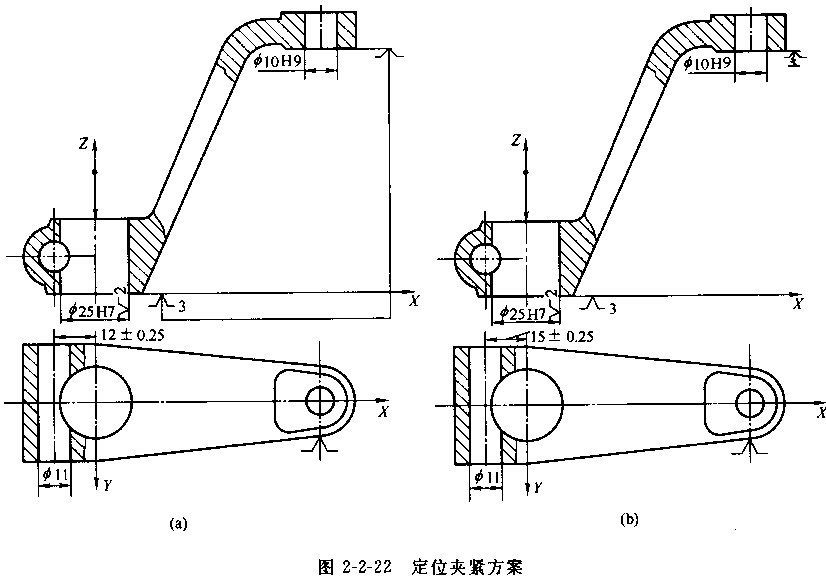
(2)选择定位元件。
①选择带台阶面的定位销,作为以φ28H7孔及其端面的定位元件,如图2-2-23所示。定位副配合取 。
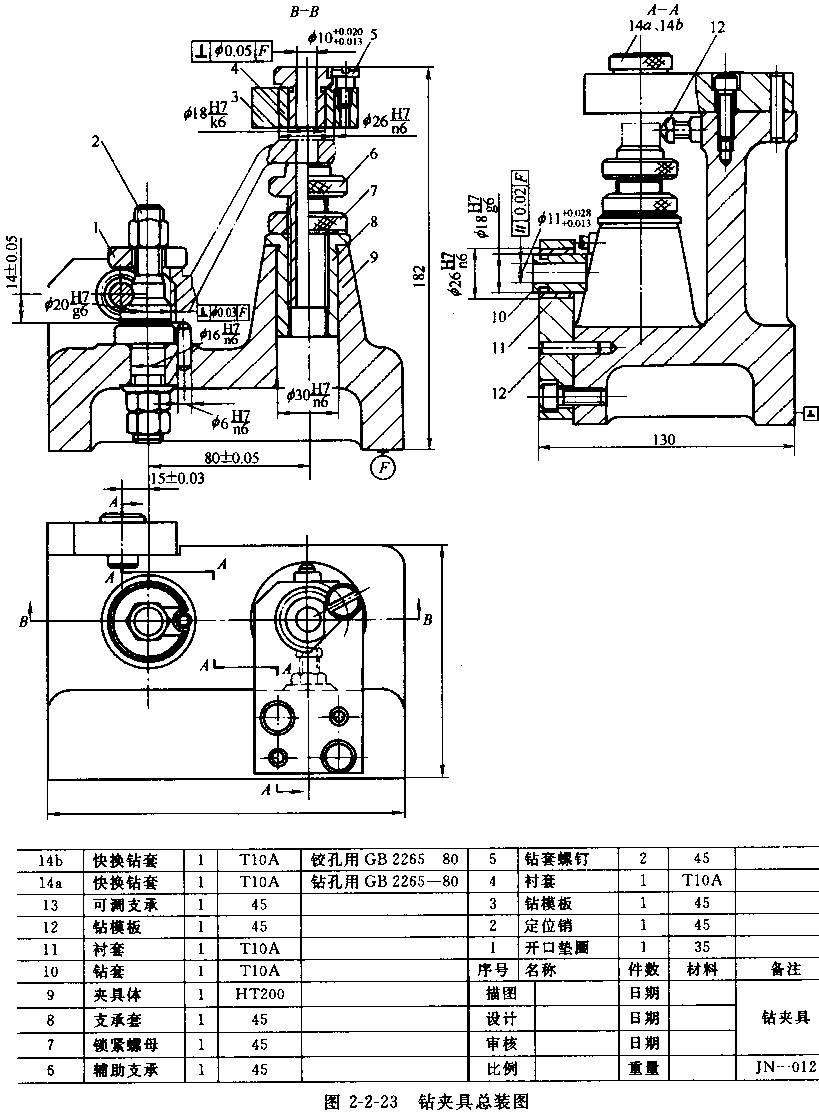
②选择可调支承钉为φ11孔外缘毛坯一侧防转定位面的定位元件,如图2-2-24(a)所示。也可选择如图2-2-24 (b)所示移动V形块。考虑结构简单,现选用图2-2-24(a)所示结构。
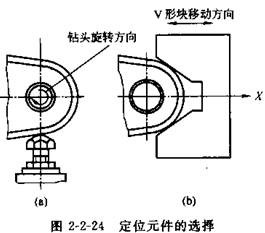
(3)定位误差计算
①加工φ10H9孔时孔距尺寸(80±0.2)mm的定位误差计算。
由于基准重合,故ΔB=0。
基准位移误差为定位孔(φ38 mm)与定位销(φ38 mm)的最大间隙,故ΔY=(0.021+0. 007+0.013)mm=0.041rnm。
由此可知此定位方案能满足尺寸(80±0.2)mm的定位要求。
②加工φ10H9孔时轴线平行度0.3mm的定位误差计算。
由于基准重合,故ΔB=0。
基准位移误差是定位孔φ28H7与定位面K间的垂直度误差。故ΔY=0. 03mm。
此方案能满足平行度0. 3mm的定位要求。
③加工φ11孔时孔距尺寸(15±0.25)mm。加工φ11孔时与加工φ10H9孔时相同。
此方案能满足孔距(15±0.25) mm的定位要求。
4.确定夹紧方案
参考夹具资料,采用M12螺杆在φ28H7孔上端面夹紧工件。
5.确定引导元件(钻套的类型及结构尺寸)
⑴对φH9孔,为适应钻、铰选用快换钻套。
主要尺寸由《机床夹具零、部件》国家标准GB/T2263-80, GB/T2265-80选取。钻孔时钻套内径φ10 mm、外径φ15 mm;衬套内径φ15 mm,衬套外径φ22 mm。钻套端面至加工面的距离取8mm。
麻花钻选用φ9. 8 mm。
(2)对φ11孔,钻套采用快换钻套。钻孔时钻套内径φ11 mm、外径φ18 mm,衬套内径φ18 mm,外径φ26 mm;钻套端面至加工面间的距离取12mm。
麻花钻选用φ10. 8 mm。
各引导元件至定位元件间的位置尺寸分别为(15±0.03)mm和(18±0. 05)mm,各钻套轴线对基面的直线度允差为0.02mm。
6.夹具精度分析与计算
由图2-2-22可知,所设计夹具需保证的加工要求有:尺寸(15±0.25)mm;尺寸(80±0.2)mm;尺寸14mm及φ10H9孔和φ28H7孔轴线间平行度允差0.3mm等四项。除尺寸14mm,因精度要求较低不必进行验算外,其余三项精度分别验算如下。
(1)尺寸(80±0.2)mm的精度校核。
定位误差ΔD,由前已计算,已知Δ=0.041mm。
定位元件对底面的垂直度误差ΔA=0.03mm。
钻套与衬套间的最大配合间隙ΔT1=0. 033mm。
衬套孔的距离公差ΔT2=0.1mm。
麻花钻与钻套内孔的间隙X2=0.050mm。
衬套轴线对底面(F)的垂直度误差ΔT3=0. 05mm。
因而该夹具能保证尺寸(80±0. 2)mm的加工要求。
(2)尺寸(15±0. 25)mm的精度校核。
ΔD=0. 041mm,ΔA=0. 03mm,ΔT1=0. 033mm。
衬套孔与定位元件的距离误差ΔT2=0.06mm。
麻花钻与钻套内孔的间隙X=0.061mm。
因而尺寸(15±0.25)mm能够保证。
(3)φ10H9轴线对φ25H7轴线的平行度0.3mm的精度校核。
ΔD=0. 03mm,ΔA=0. 03mm。
衬套对底面(F)的垂直度误差ΔT=0. 05mm。
因而此夹具能保证两孔轴线的平行度要求。
7.绘制夹具总图
根据已完成的夹具结构草图,进一步修改结构,完善视图后,绘制正式夹具总装图,如图2-2-23所示。
8.绘制夹具零件图样
从略。
9.编写设计说明书
从略。
铣床夹具设计实例
图2-2-25所示为轴套类零件的零件图样。现需设计铣两槽5 mm的铣夹具。
1.零件本工序的加工要求分析
本工序的加工要求,在实体上铣出两通槽,槽宽为5 mm,槽深为27 mm,两槽在圆周方向互成60°±30′角度,表面粗糙度为Ra1. 25μm。
本工序之前,外圆φ60 mm、内孔φ32 mm及两端面均已加工完毕。
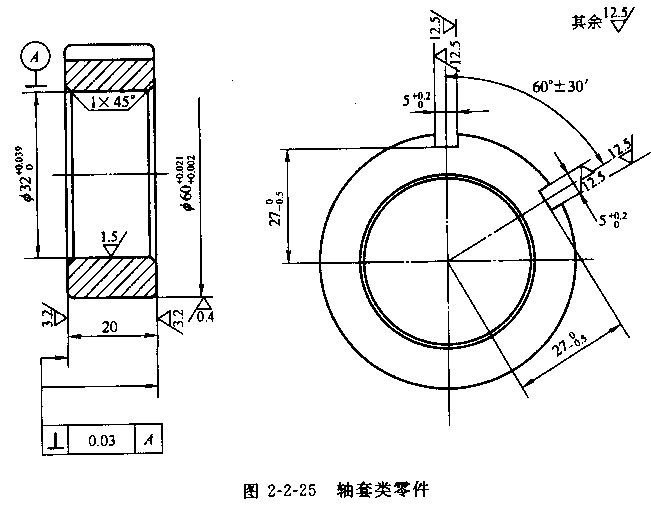
本工序采用φ5mm标准键槽铣刀在X5l立式铣床上,一次装夹六件进行加工。
2.确定夹具类型
本工序所加工的是两条在圆周互成60°角的纵向槽,因此宜采用直线进给带分度装置的铣夹具。
3.拟定定位方案和选择定位元件
(1)定位方案。
①以φ32 mm内孔作为定位基准,再选孔端面为定位基准,限制工件五个自由度。如图2-2-26(a)所示。
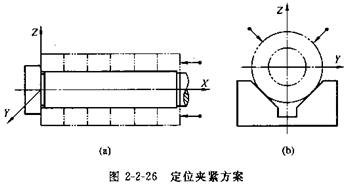
②以φ60 mm外圆为定位基准 (以长V形块为定位元件),限制4个自由度。如图2-2-26 (b)所示。
方案②由于V形块的特性,所以较易保证槽的对称度要求,但对于实现多件夹紧和分度较困难。
方案①的不足之处是由于心轴与孔之间有间隙、不易保证槽的对称度,且有过定位现象。但本工序加工要求井不高,而工件孔和两端面垂直精度又较高,故过定位现象影响不大。
经上述分析比较,确定采用方案①。
(2)选择定位元件。根据定位方式,采用带台肩的心轴。心轴安装工件部分的直径为φ32g6( )mm,考虑同时安装6个工件,所以这部分长度取112mm,由于分度精度不高,为简化结构,在心轴上做出六方头,其相对两面间的距离尺寸取28g6( )mm,与固定在支座上的卡块槽28H7( )mm相配合;加工完毕一个槽后,松开并取下心轴,转过相邻的一面再嵌入卡块槽内即实现分度。心轴通过两端φ25H6mm柱部分安装在支座的V形槽上,并通过M16螺栓钩形压板及锥面压紧,压紧力的方向与心轴轴线成45°角。
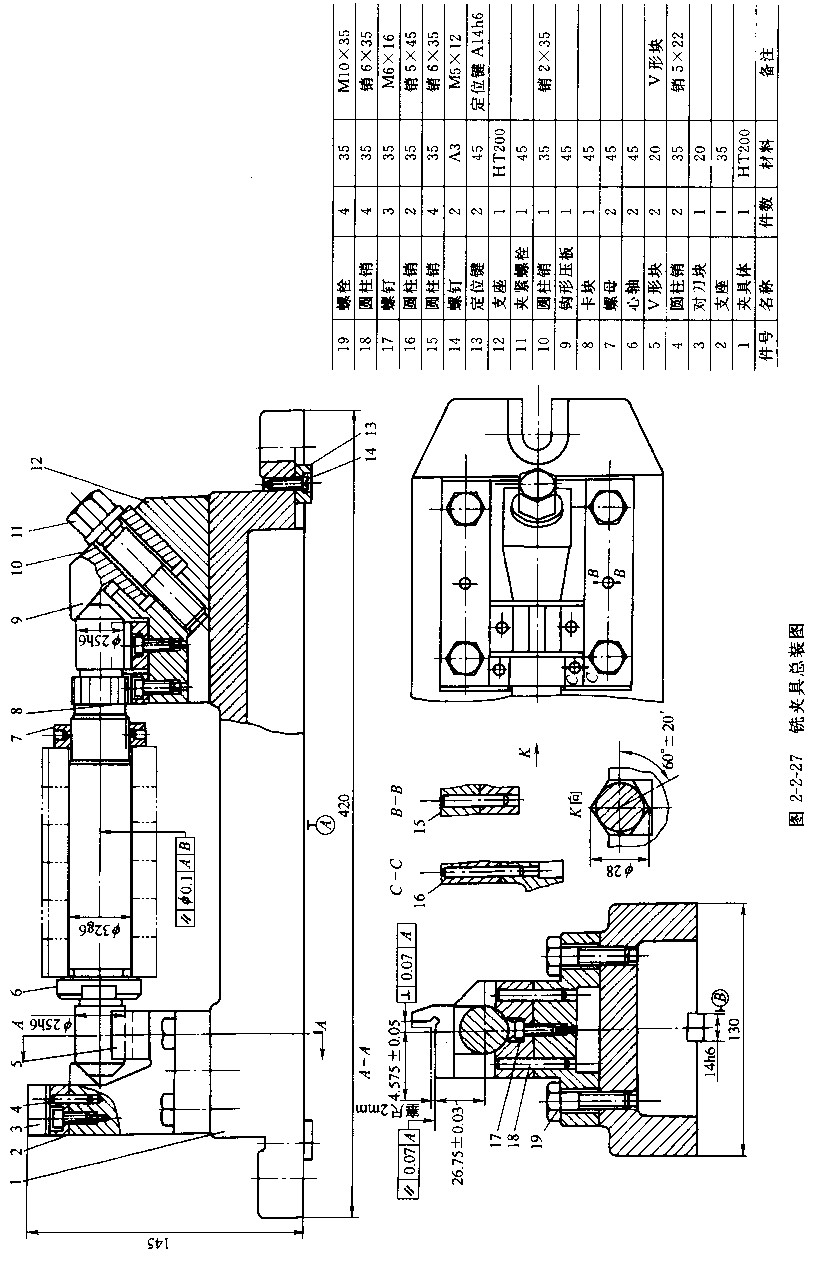
(3)定位误差计算。工序尺寸27 mm 定位误差分析如下。
由于基准重合ΔB=0
由于定位孔与心轴为任意边接触,则因此定位精度足够。
由于加工要求不高,其他精度可不必计算。
4.确定夹紧方案
根据图2-2-26所示心轴结构,用M30螺母把工件轴向夹紧在心轴上。心轴的具体结构如图2-2-27所示。
5.确定对刀装置
(1)根据加工要求,采用GB/T2242-80直角对刀块;塞尺符合GB/T2244-80,基本尺寸及偏差2 mm。
(2)计算对刀尺寸H和B
如图2-2-28所示,计算时应把尺寸化为双向对称偏差,即
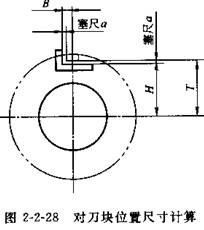
6.夹具精度分析和计算
本夹具总图上与工件加工精度直接有关的技术要求如下。
定位心轴表面尺寸φ32g6。
定位件与对刀间的位置尺寸(24.75±0.08)mm,(4.575±0.05)mm。
定位心轴安装表面尺寸φ25h6。
对刀塞尺厚度尺寸2 mm。
分度角度60°±10′。
定位心轴轴线与夹具安装面、定位键侧平面间的平行度公差为0. lmm。
分度装置工作表面对定位表面的对称度公差为0. 07mm。
分度装置工作表面对夹具安装面垂直度公差为0.07mm。
对刀装置工作表面对夹具安装面的平行度和垂直度公差为0. 07mm。
(1)尺寸27 mm的精度分析。
ΔD=0. 064mm(定位误差前已计算)。
ΔT=0. 16mm(定位件至对刀块间的尺寸公差)。
ΔA= ×20mm=0.0086mm(定位心轴轴线与夹具底面平行度公差对工件尺寸的影响)。
故此夹具能保证27 mm尺寸。
(2)对60°±30′的精度分析。
分度装置的转角误差可按下式计算。
故此分度装置能满足加工精度要求。
7.绘制夹具总图
图2-2-27所示为本夹具的总装图样。
8.绘制夹具零件图样
从略。
9.编写设计说明书
从略。
夹具设计实例信息由思诚资源网提供,有需要请点击EROWA夹具